As we enter into Craft Week 2023, we introduce QEST a charity dedicated to the support, education and training of the nation’s most gifted makers. Known for his keen advocacy of craftsmanship, the former Prince of Wales, now King Charles III has been the charity’s Patron since 2017.
Craft Week 2023: The Incredible Story of QEST
11th May 2023
As part of Craft Week 2023, The Queen Elizabeth Scholarship Trust (QEST) is partnering with Artefact to show the intricate artisanal works from their most talented scholars. Here, Sphere discovers the incredible royal story behind QEST, and meets its star artisans.
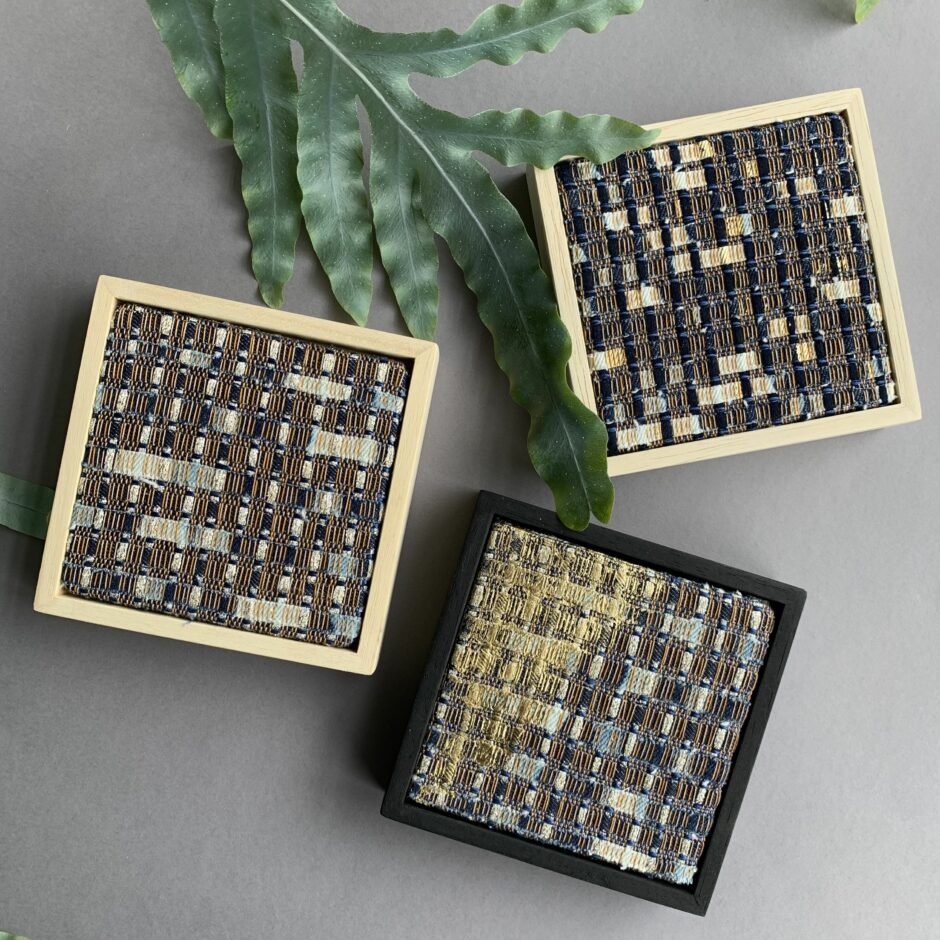
Sustaining both traditional and contemporary crafts, QEST supports a diverse and beguiling array of artisanal skills, numbering some 130 in total. Disciplines range from the familiar — ceramics, glasswork, silversmithing and wood sculpture — to the more niche, such as armoury, thatching and puppet-making. As artisans know all too well, the mastery of any craft requires highly advanced skills, coupled with in-depth knowledge and expert training.
To be considered for funding, applicants must demonstrate outstanding talent in their field. Scholarships are granted to established artisans looking to reach new heights in their craft, while apprenticeships are given to promising individuals wanting to learn from the best. Funding is used to support everything from college courses and vocational training to hands-on apprenticeships or one-on-one tuition under a master craftsperson. Even after financial support ends, QEST continues to support the careers and crafts of its alumni, creating new opportunities for makers to network, collaborate and exhibit their work.
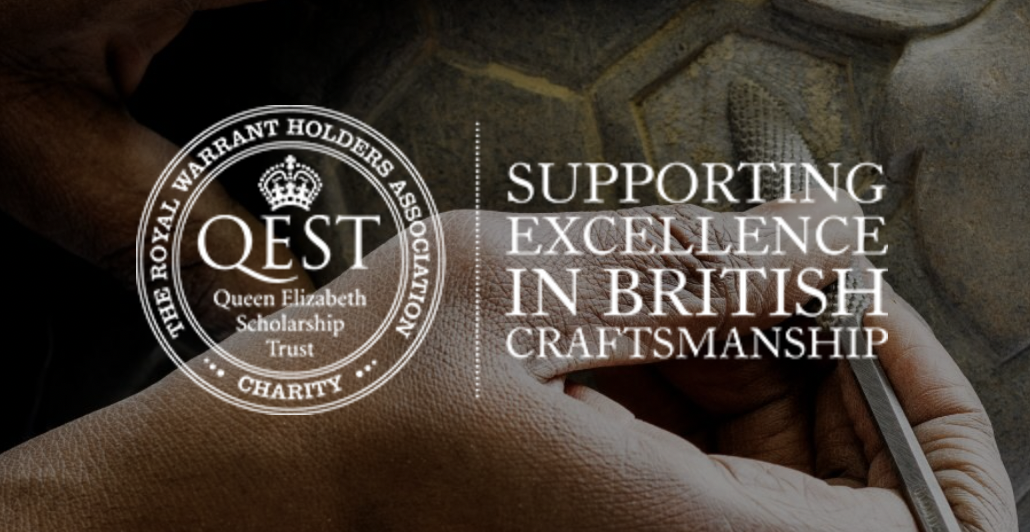
It is no exaggeration to state that QEST’s support is vital to the nation’s time-honoured craft skills — ensuring they are preserved with proper investment in the training of the next generation of makers — as well as the ongoing evolution of Britain’s cultural heritage. The works of QEST scholars Laura Quinn, Tom Palmer, Justyna Medon, Lucy May Schofield, Tom Vaughan and Hannah White will be exhibited at Artefact from 9-13 May.
In further celebration of Craft Week, here we showcase a selection of extraordinary crafts practised by some of QEST’s other talented artisan makers.
QEST Shoemaking - Oluwamuyiwa Fadairo
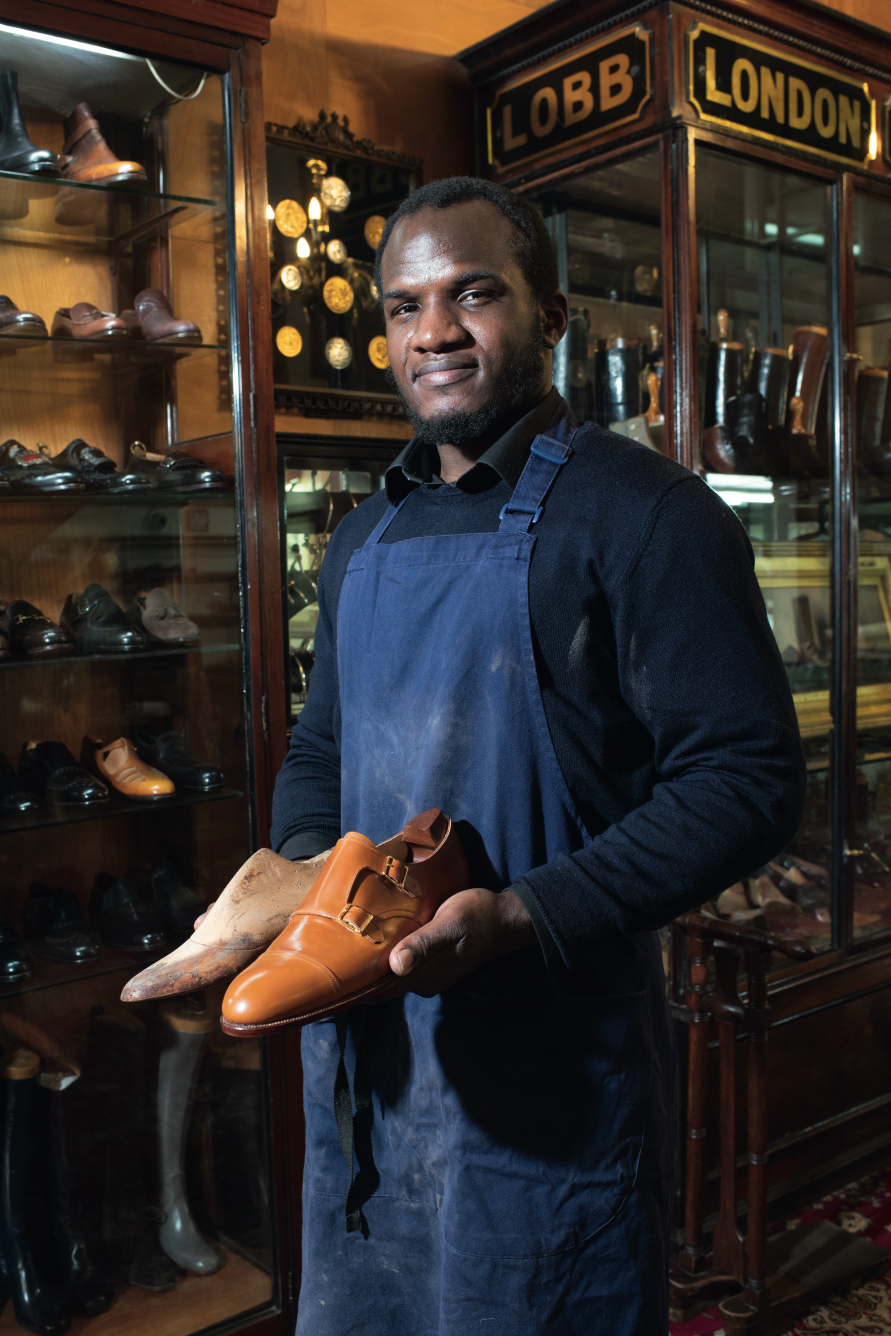
A precise and exacting craft, bespoke shoemaking requires both skill and an infinite amount of patience, as Oluwamuyiwa Fadairo has discovered during his three-year QEST apprenticeship at heritage shoemaker John Lobb. Making a pair of hand-welted shoes, which involves hand-stitching the upper, insole and welt together via a single seam, takes weeks and involves close to 200 steps. The intricate processes include hand skiving, hand lasting, heel building, balancing uppers on shoe lasts, boot construction and finishing. It is also vital to master the craft’s specialist tools; Fadairo is adamant that having properly sharpened knives is essential to achieve the very best results.
QEST Armoury - Graham Ashford
Although there is little call for medieval armour on the battlefield these days, the centuries-old craft is actively practised by those with a passion for the past. Making historically accurate reproduction armour requires advanced metalwork skills such as forging, cutting, planishing (flattening) and assembling. Whether the craftsperson is making a helmet, a gauntlet or a full suit, each piece should be wearable without hindering movement, requiring dexterity with details such as hinges and overlapping sections. Having practised the craft for years as a hobby, Graham Ashford left his IT career behind to become a professional armourer, creating bespoke armour for collectors, re-enactors and museums.
QEST Hand weaving - Momoka Gomi
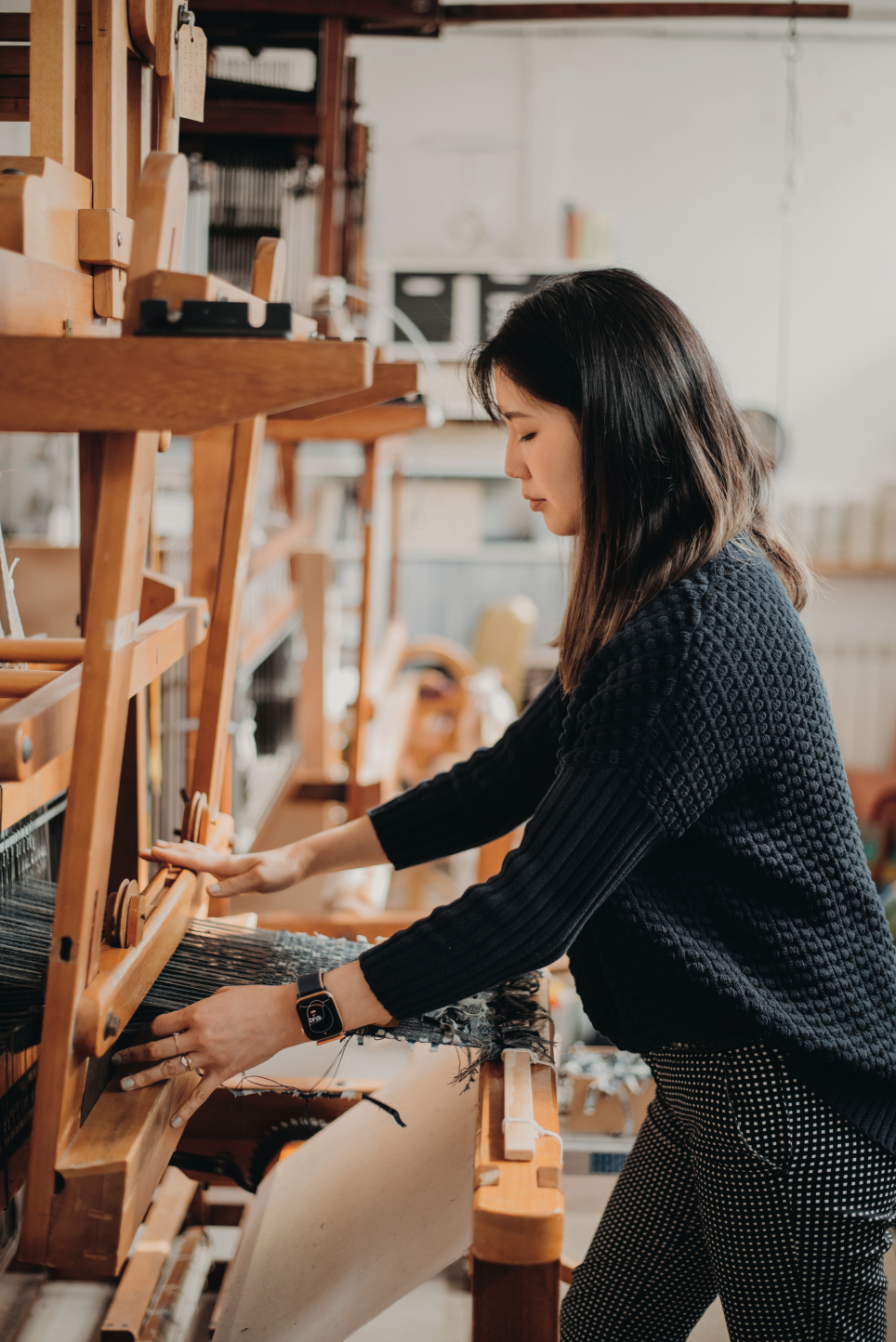
This time-intensive craft creates fabric through the interlacing of threads placed at intersecting angles on a loom: a frame that supports the threads. Vertical threads, known as the warp, are held in place on the loom while horizontal threads — the weft — are woven through them to produce intertwined rows. The technique is commonly used to create patterned fabric, with different results achieved by varying the type of yarn used and the spacing between warp threads. As a result of her QEST Scholarship, hand weaver Momoka Gomi hopes to push her work to new heights and create bespoke fabric art that is both sculptural and wearable.
QEST Mosaic making - Gary Drostle
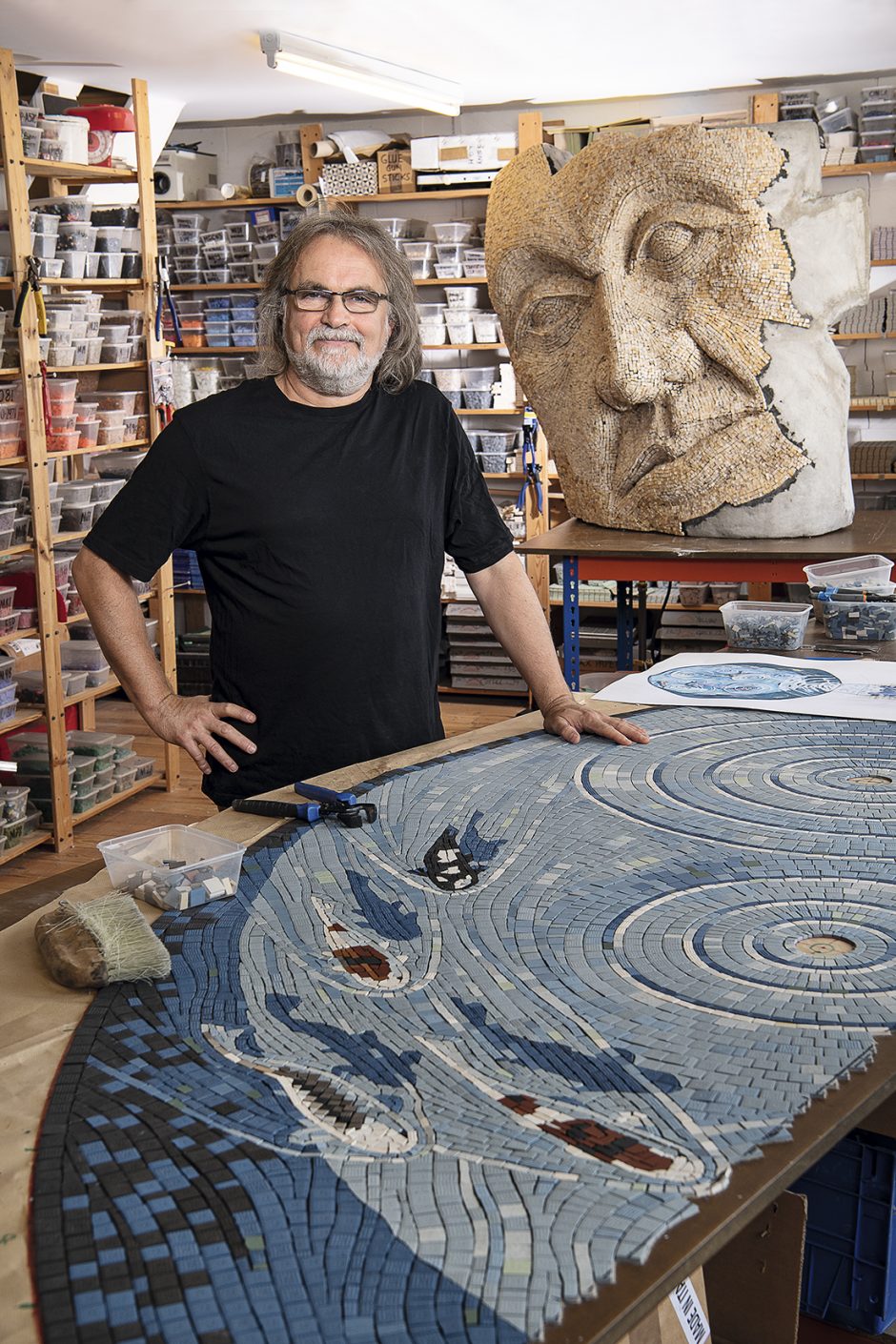
Through the careful assembly of tesserae (small pieces of stone, glass or ceramic) on plaster or mortar, mosaics are used to decorate surfaces with intricate scenes and patterns. The process involves creative design, cutting and laying the tesserae, and grouting and cleaning to finish. The craft is recognised as among the most ancient art forms and, while the Romans were famously fond of mosaic, it is thought to have originated in Mesopotamia. Artisans such as Gary Drostle, renowned for his mosaic-encrusted sculptures and signature fishpond creations, keep the practice going through commissioned installations, public murals and practical workshops.
QEST Farriery - Nina Thomas
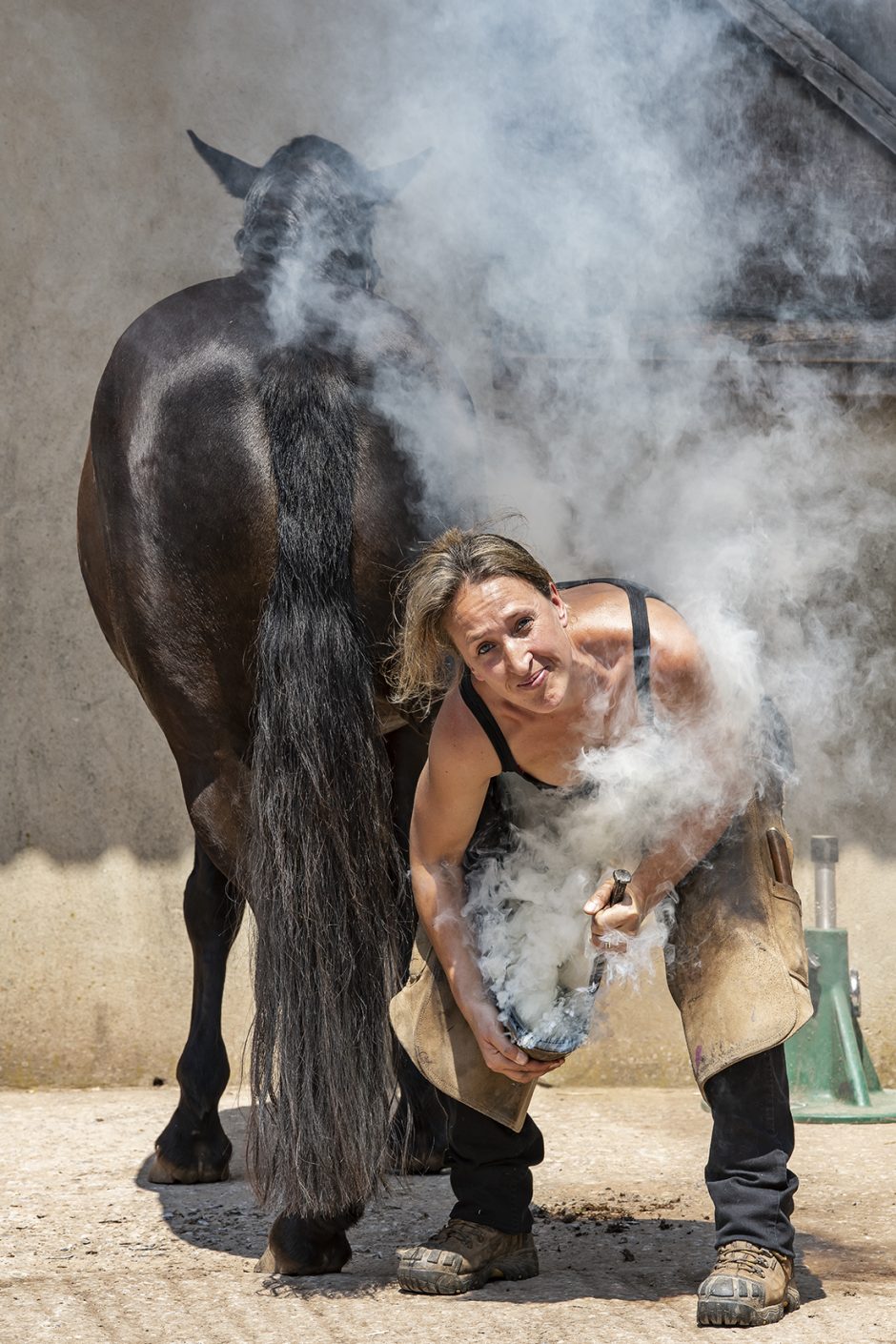
The method of making and fitting horseshoes, farriery also involves cleaning, trimming, and shaping hooves. Combining blacksmithing with veterinary skill, farriers create custom horseshoes using expert knowledge of equine physiology. Not only does ironwork require strength and resilience, but farriers must also be able to communicate well with horses. Used for a variety of reasons, including farming, driving, show jumping and dressage, working horses require re-shoeing every five to eight weeks to maintain correct balance and optimum performance. As a result, professional farriers like Nina Thomas might craft up to 100 shoes a week. Although she has accumulated 20 years of farriery experience, there will always be more for Thomas to learn, as every horse is different.
QEST Ceramics - Frances Priest
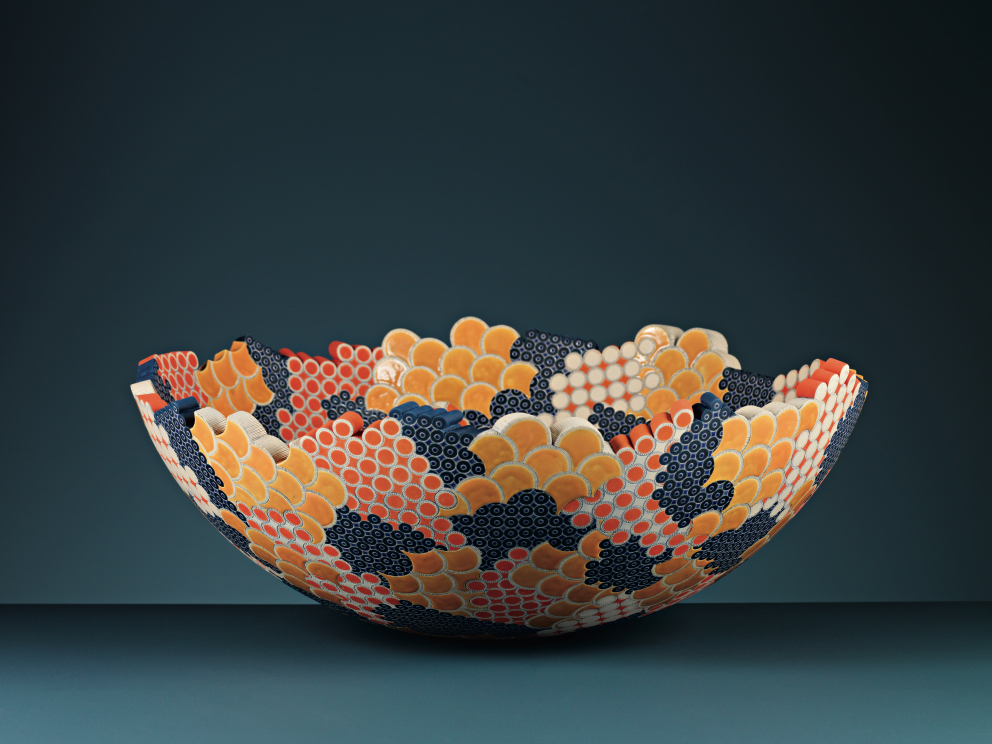
Drawing on earth, air, fire and water, the ancient practice of ceramic making dates back thousands of years. Many of the elemental methods used to craft ceramics today are the same as those used by our ancestors. Raw earthen materials, such as clay, are combined with water and shaped, by hand, on a wheel, or with moulds; the pieces are then dried, and fired in a kiln. At this point, items can be glazed to add colour and shine. A maker known for exploring acultural histories with her intricate patterned ceramics, QEST Scholar Frances Priest is currently learning the heritage manufacturing skills of encaustic and moulded tile manufacture.
QEST Millinery - Filipa Cardoso
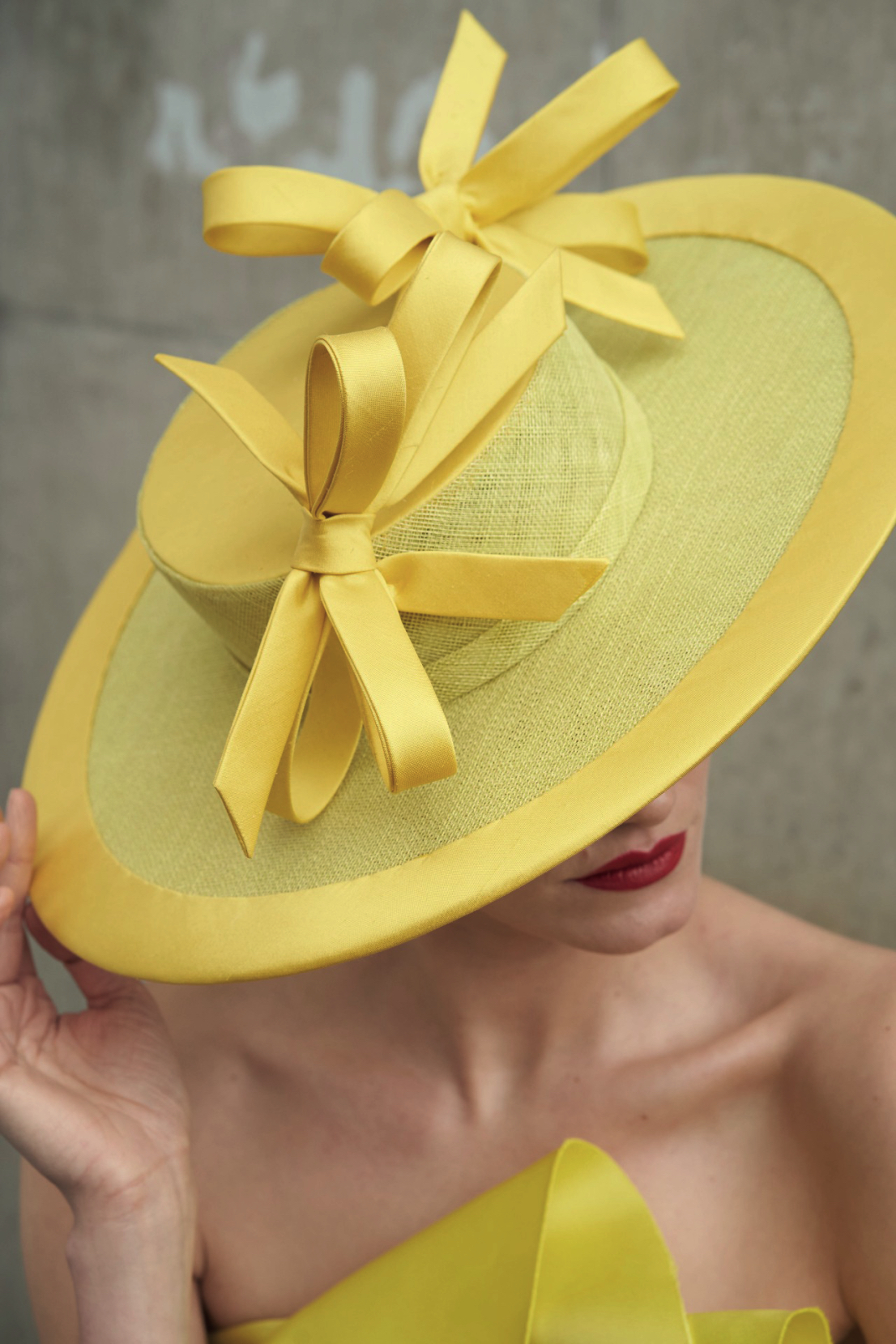
Millinery is the fine art of creating elegant hats. While women no longer wear hats on a daily basis as a matter of course, traditional bespoke millinery remains in demand for special occasions such as weddings and the British social season. Distinctive, stylish and often highly creative, these hats can be crafted using a wide array of materials — including felt, silk, straw and buckram — and decorated with trimmings, such as feathers and veils. As a QEST Apprentice, Filipa Cardoso is learning to elevate her contemporary designs with technical skills, including blocking silhouettes on a cast, manipulating sinamay fibres to create a foundation, dyeing materials, and wiring edges to keep them in shape.
QEST Luthiery - Tom Sands
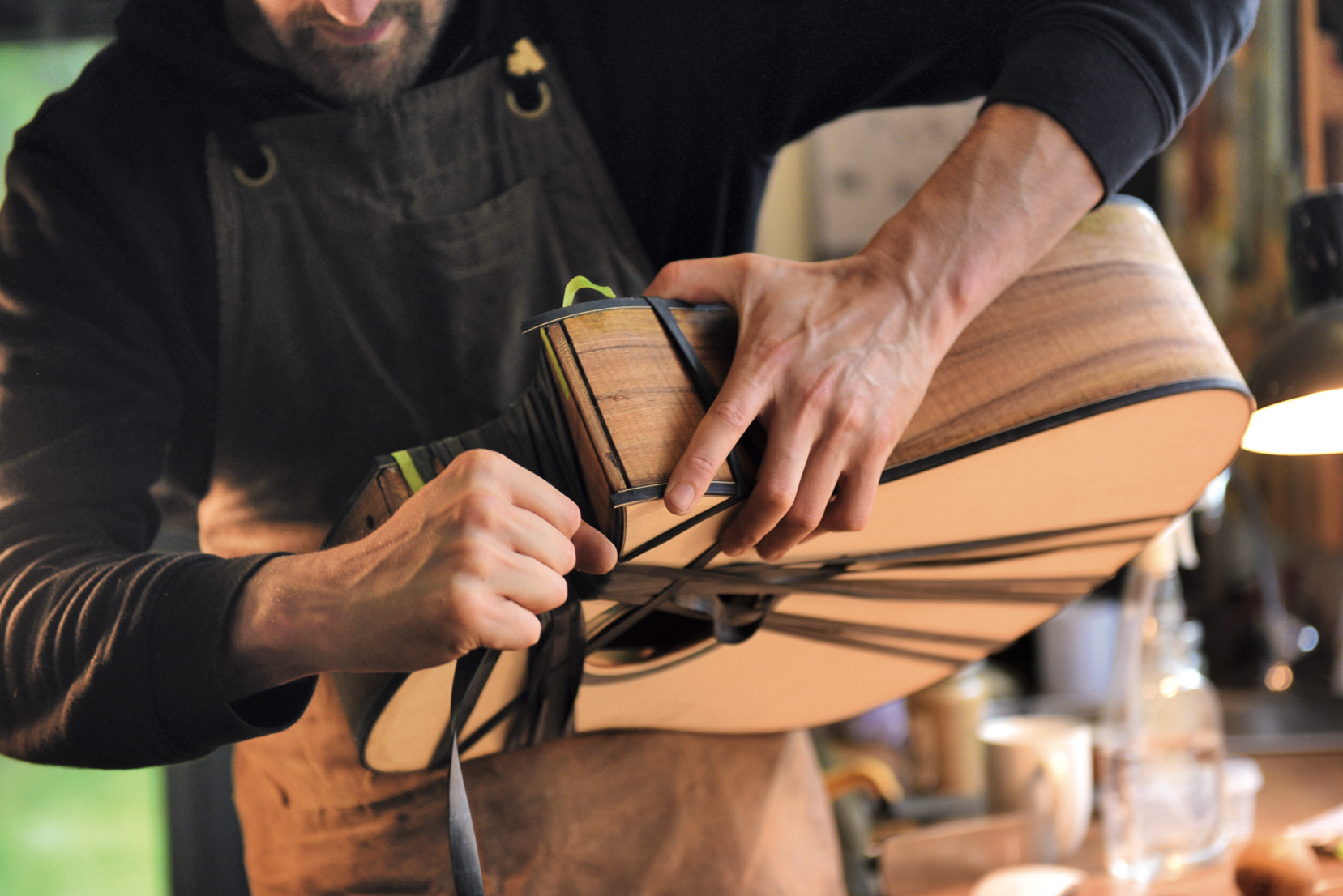
A luthier makes string instruments with a neck and sound box, such as guitars, violins and lutes. Creating these instruments is complex; each requires a component-based, structurally sound design made from wood worked at a remarkably high standard. Multiple processes are involved, from gluing, bending and joining wood to shaping frets, spacing strings and applying decorative inlays or ornamentation. QEST alumnus Tom Sands learned under world-renowned master luthier Ervin Somogyi in Oakland, California, as part of his scholarship, and now has his own workshop in North Yorkshire.